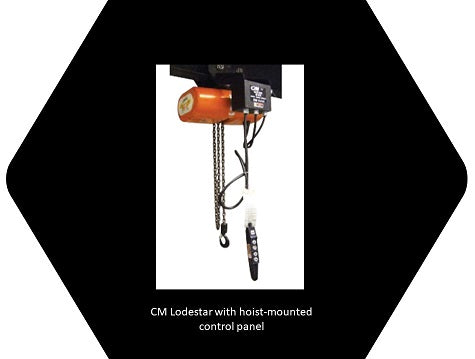
Can you remove hoist-mounted controls and remotely mount the same controls?
Andrew T. Litecky
Welcome to The Hoist Guy's Blog, where our resident Hoist Guy, Andrew T. Litecky, shares his knowledge and experience of many years in the overhead material handling industry, including information about hoist controls and some key considerations when remotely mounting a hoist control enclosure.
Can you remove hoist-mounted controls and remotely mount the same controls?
We recently sold a CM Lodestar to our customer for a “gray area”, adjacent to a clean room, including a festooning system for a thirteen-foot monorail. Documentation for the customer’s approval included a hoist outline diagram, a wiring diagram and a general arrangement showing the hoist and the beam with festooning. These submittals were marked “approved” and the order shipped out.
Several months later, the hoist was installed, and we got a call from the site. A process pipe was in close proximity to the monorail, and the hoist-mounted control enclosure could not pass. This interference prevented the hoist from making a critical pick.
The site contractor asked: “Can we remove the main control enclosure and remotely mount it to eliminate the interference along the monorail?” The answer is yes, but there are specific considerations which must be assessed.
Key Considerations When Remotely Mounting a Hoist Control Enclosure
Before removing hoist-mounted controls and remotely mounting those same controls, there are a few things that must be considered.
- Wiring Adjustments: When the control enclosure is removed from the hoist, wires that ended on the controls had to be terminated elsewhere. A junction box was mounted on the hoist in place of the control enclosure. In this case, the junction box had to be the right size to accept all the control wires as well as get past the interfering process pipe.
- Festooning Adjustments: Since the current festooning system had only 4 conductors (L1, L2, L3, ground), additional power conductors were required. They include three (3) “T” leads for the hoist motor, three (3) “T” leads for the trolley motor, two (2) leads for the hoist brake and two (2) leads for the trolley brake. Additional control conductors would include two (2) upper limits, (2) lower limits, (2) for the hoist thermal Klixon, (2) for the trolley thermal Klixon. Luckily, the original festoon system trolleys were large enough to accept the extra festooning conductors
- Rebalancing the Hoist: The last item on the list was balancing the hoist on the monorail. The original hoist, made by CM in their Damascus, Virginia factory, was balanced for a monorail system. However, after removing the large control box, counterweights were required to rebalance the hoist. Field balancing of a hoist, crucial for its successful operation, can only be done by trial and error.
The Resolution: Wall Mounted Hoist Controls with Additional Festooning
After making these changes, the hoist and motor driven trolley moved along beam to the required lift points and avoided the obstruction. The same junction box and control panel that had been mounted on the hoist were relocated to a nearby wall and connected through additional festooning. See the below drawings that show the before and after configurations.
This case shows that a delay between approval drawings and installation requires strong communication among the trades. Project management needs to make everyone aware of the operating space around the hoist with trolley as it moves along the beam.
Innovative Engineering & Problem Solving with Shupper-Brickle
Since 1969, Shupper-Brickle Equipment has specialized in hoists and engineered lifting systems. From complete analysis and custom design of bridge cranes and overhead material handling systems to modernization, upgrades and repairs, our innovative engineers can solve any lifting problem, no matter how unusual or unique. Contact us for questions about your lifting application or read our Top 10 Rules for Architects and Engineers and our other Case Study blog posts.